21 May 2025
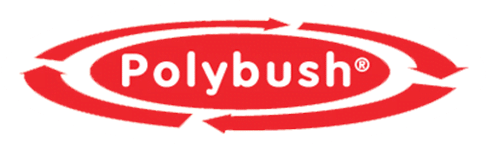
Speak to one of our experts.
28 February 2024
There are certain bushes on popular cars that fail time after time. For example, the MK7 Fiesta rear beam bush and the VAG front wishbone rear bush. These bushes are often difficult to replace, costing you time and money. Worse, your customers get fed up with the problem and fitting rubber bushes doesn’t solve it. Polybush has the solution. Polyurethane bushes that last four to five times longer than the originally fitted bushes.
Why does Polybush solve the problem? Because rubber bushings have issues; from compression set to vulnerability to oil, fuel, and road grime. Rubber can rip, de-bond, and lose structural integrity over time, often very quickly. In contrast, Polyurethane excels at every step. Polybush describes its products as the superheroes of suspension bushes, “impervious” to compression set, oil, fuel, and road salts, offering a level of reliability that rubber can “only dream of”.
What do polyurethane bushes offer?
1. Longer lasting: Polybush products provide increased longevity. For example, solutions for Mondeo Mk4’s rear trailing arm bushes or Astra MK6 Rear Beam bushes outlast their rubber counterparts by four to five times. The firm engineer’s solutions with mechanics in mind, tackling notorious headache points.
2. Improved control: Installing polyurethane bushes injects a shot of adrenaline into your steering system. Your customers will experience a tighter, more precise connection between the steering wheel and the road.
3. Increased tyre life: Polybush saves your customers money by reducing tyre wear and installation time, and offering a fit-and-forget product. We’re putting money back in everyone’s pocket.
4. Comfort: Worried that upgrading to Polyurethane might sacrifice the comfort your customers love? Fear not. Polyurethane can match the original hardness of “normal” cars, ensuring no compromise on the smooth, comfortable ride your customers expect.
5. Easy to fit: But we can hear you thinking, “what about installation?” No special tools are required, remove the rubber bushes as you usually would and most bushes just push in by hand, then simply use a vice or hammer to drive the centre tube home.
Over twenty years ago the UK’s biggest bus manufacturer was faced with rubber anti-roll bar (ARB) link bushes failing after only three to four months. They asked Polybush to produce the same part in polyurethane. They then pitted Polybush against their current rubber bush at the Millbrook Proving Ground in Bedfordshire. The results?
■ The rubber vehicle suspension bushes failed after 5,000 to 15,000 cycles
■ Polybush’s polyurethane vehicle suspension bushes lasted 55,000 cycles
■ Polybush’s polyurethane vehicle suspension bushes were measured at 10 to 15°C cooler than the rubber bush while operating on the test bed.
■ When fitted to the bus Polybush’s polyurethane vehicle suspension bushes did not change the ride of the vehicle.
■ Polybush has been supplying these bushes on new build and for spare parts for 20 years replacing all the ARB system rubber bushes with polyurethane.
In another example Polybush solved the problem of permanent compression set a vehicle builder was having with their standard rubber bushes. These bushes were permanently compressing under load and then splitting radially. Polybush ran trials to compare this 65°A rubber bush with two Polybush grades 65°A, i.e., the same hardness and 75°A, 10 points harder.
The three samples were compressed at 30mm per minute to 50 per cent of their original thickness and relaxed at the same rate. This cycle was repeated without interruption over 20 cycles.
The actual force and reduction in force between the first and last cycle were: The table shows how quickly the rubber vehicle suspension bush permanently compresses compared to the equivalent hardness of Polybush. Once in this state, the rubber bush’s resilience and ability to flex is greatly reduced causing splitting and failure.
OE supplier:
Polybush is an original equipment supplier to a wide range of vehicle builders. Polybush make polyurethane suspension parts for road sweepers, heavy fork lift trucks, earth moving machines, electric vehicles, buses and tractors.Polybush also supplies to companies upgrading vehicles. This can be for armoured 4 x4 luxury cars or upgrades of standard vehicles for military and para military purposes.
We also supply to armies and police forces who need longevity in the field by switching from rubber to polyurethane.
Polybush makes all the polyurethane and steel parts at its factory in Wrexham, North Wales. This includes all the computer aided design of the parts and the necessary tooling. Once designed all the tooling is again made in-house using computer aided manufacturing on our Mazak milling and turning centre machines.
So, why polyurethane for your suspension bush requirements? Polyurethane blends combine high tensile strength with elasticity, delivering durability that rubber can’t. It resists wear, resists oils and fuels, and remains resilient in the harshest conditions.
Polyurethane doesn’t age, it bounces back effortlessly, and it can take the heat – literally, with a service temperature range from –40°C to +80°C.
21 May 2025
1 May 2025